History of hot-dip galvanizing
Galvanization of metal parts and structures is done in order to prevent corrosion and more resistance to weather effects. The background of this knowledge goes back to the years 1737 to 1798, when an Italian scientist in 1775 from BOLOGENS University as a professor of this university in the field of The professor of this university in the field of anatomy discovered by chance that the leg of a dead frog moves when a piece of metal touches it. In this way, he found out that metals create an electrochemical effect on living organisms. Galvani published the results of his work in 1791. He paved the way for making big decisions among scientists in this field. As far as Volta also proposed an opposite idea, he thought that the reason for this issue was the metal arc.
Hot dip galvanization is a method of coating with zinc metal, and finally, the coating process forms a chemical bond between iron and zinc. Hot dip galvanization is, in simple terms, a coating that is formed on iron or steel that is suitable for galvanizing in terms of composition and design by dipping it in a bath of molten zinc. Hot dip galvanization has been used for nearly 150 years. . Most of the zinc produced in the world is used for coating. The most important reason for the resistance of zinc to natural decomposition is the nature of its resistance.
Benefits of hot galvanizing
Low cost
There is a general rule in business that whoever produces good quality at low cost wins. In many cases, galvanization is the cheapest method compared to other coating methods. Currently, the cost of galvanization is lower than the cost of painting, and alternative coatings, especially painting, are more expensive than galvanization. Man-hours (manpower) to cover less.
Ability to respond quickly
When corrosion protection can be achieved in minutes by hot-dip galvanizing, you need several weeks for painting and you have to wait for good weather conditions. In hot galvanizing, corrosion protection occurs in the same galvanizing plant, and you can move the parts to another place for installation and assembly. You don’t need to pay for shipping again
Ease of checking quality
Checking is the control of coating thickness based on ISO1461-ASTM A123 – ISIRI standards. Tests are performed by micrometers or non-destructive methods. For this reason, galvanized steel is more resistant to mechanical damage resulting from transportation, storage, and assembly, and this allows galvanized steel to be transported to any country, and due to the good resistance of galvanized steel, it can be used for designing in areas where erosion occurs. Hot galvanizing consists of immersing the steel in molten zinc, and in this way all internal and external surfaces, corners and even the edges of the surfaces and all unprotected spaces are covered by zinc, and all corners and narrow edges that are covered by paint or Spray or other coatings are poorly covered. In hot galvanization, all surfaces are well covered.
Hot galvanizing steps
The term hot galvanizing refers to the set of operations of placing iron and steel in a bath of zinc metal and creating a coating of zinc, in order to increase the life of iron or steel against corrosion, this coating is the result of a metallurgical reaction between molten zinc and existing iron It occurs in steel. This coating creates a layer with the same thickness on the entire surface of the metal. The set of this operation is shown in the figure below.
An operation that has been used since 1742 and has protected metal against corrosion at a reasonable price for many years. The three main steps in hot galvanizing operations are: 1-Surface preparation 2-Galvanization 3-Operations after galvanization, each of the above operations will be explained separately.
Surface preparation
The first step in hot galvanizing is the complete cleaning of the steel surface from any oxidation, rust, and traces of chemical substances, for this purpose, after the steel is hung by a chain and wire or a special crane, three furnaces are used to prepare and clean the surface. Steel is made in the following order.
Degreasing: In this step, the steel is first placed in a bath with degreasing acids or fat-burning solvents to remove stains, oil or grease from the surface of the steel, then the steel is rinsed.
Pickling: The steel piece is placed in a bath containing hydrochloric acid or sulfuric acid, so that the oxidized parts and small spots are separated from the steel surface. After this operation, which is called pickling, the steel is rinsed again and then to a surface preparation stage. which is called fluxing.
Fluxing: The purpose of fluxing is to clean all the oxides formed on the surface of the metal during pickling and to create a protective layer on the surface of the steel to prevent the steel from oxidizing before entering the galvanizing bath. A type of flux that is in a separate tank that is slightly acidic and contains a combination of zinc chloride and ammonium chloride. Another type of flux, which is poured on the surface of the molten zinc in the galvanizing tub, and the purpose of adding it is the same as the first type of flux, and it prevents steel from oxidizing during galvanization. After the preparation steps, i.e. degreasing, pickling and fluxing, the surface of the metal is completely cleaned of any oxidation and stains that prevent the reaction between steel and zinc in the galvanized tub.
Immersion operation
When the steel is completely cleaned, it is ready to enter the galvanized tub, the galvanized tub contains zinc according to the ASTM B6 standard. In this standard, zinc is introduced with three different grades, and the minimum purity of zinc in the galvanized tub is more than 98% in all three grades. Sometimes other metals are added to the zinc melt in the galvanizing tub to obtain the desired properties of the galvanized coating. The temperature of molten zinc in galvanized tub is usually between 438-460 degrees, at which temperature zinc is molten. After entering the galvanizing bath, the product remains in the galvanizing melt until its temperature reaches a point where the galvanized coating is formed on the steel. When the reactions between zinc and iron are complete, the galvanized steel is taken out of the galvanizing bath, which The steel coating operation usually takes less than ten minutes, which time depends on the thickness of the steel. As can be seen from the microscopic image below, the galvanized coating is shown for steel with a low silicon content and silicon impurity less than 0.04%. while the thickness of the coating is limited due to interactions between iron and zinc
Operation after galvanizing
When the steel is removed from the galvanized tub, additional operations may be needed to improve the quality of the galvanized coating. One of the most common and widely used operations is called rapid cooling. The water tank used for this operation contains some chemical additives that create a layer on the galvanized coating to protect the manufactured product during transportation and storage. Other finishing steps, which include cleaning the drops of zinc metal or slag, which are removed by sanding and grinding.
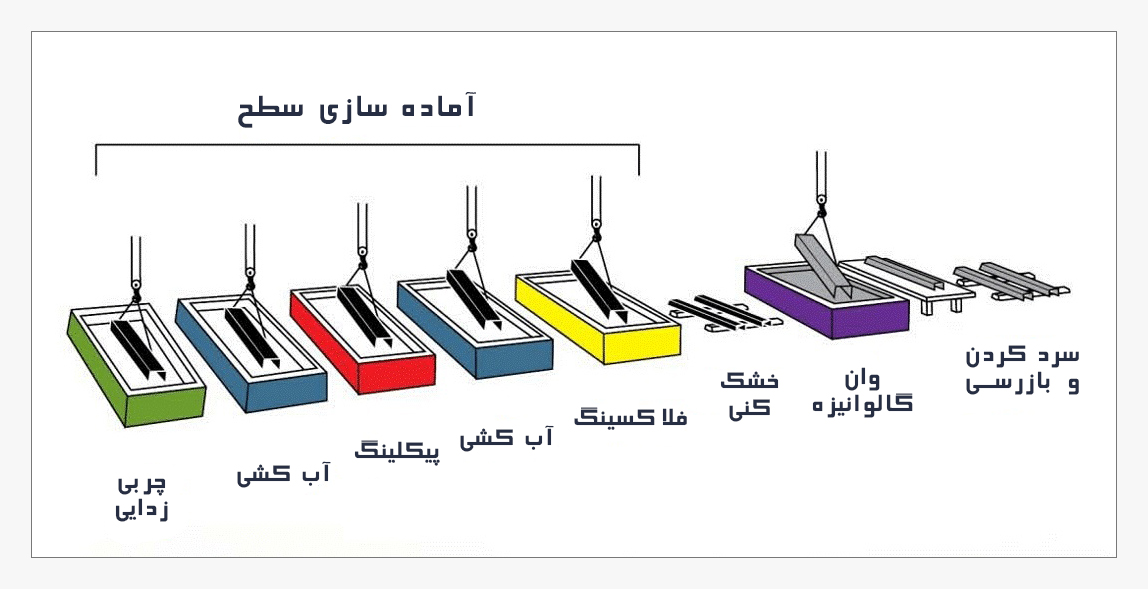
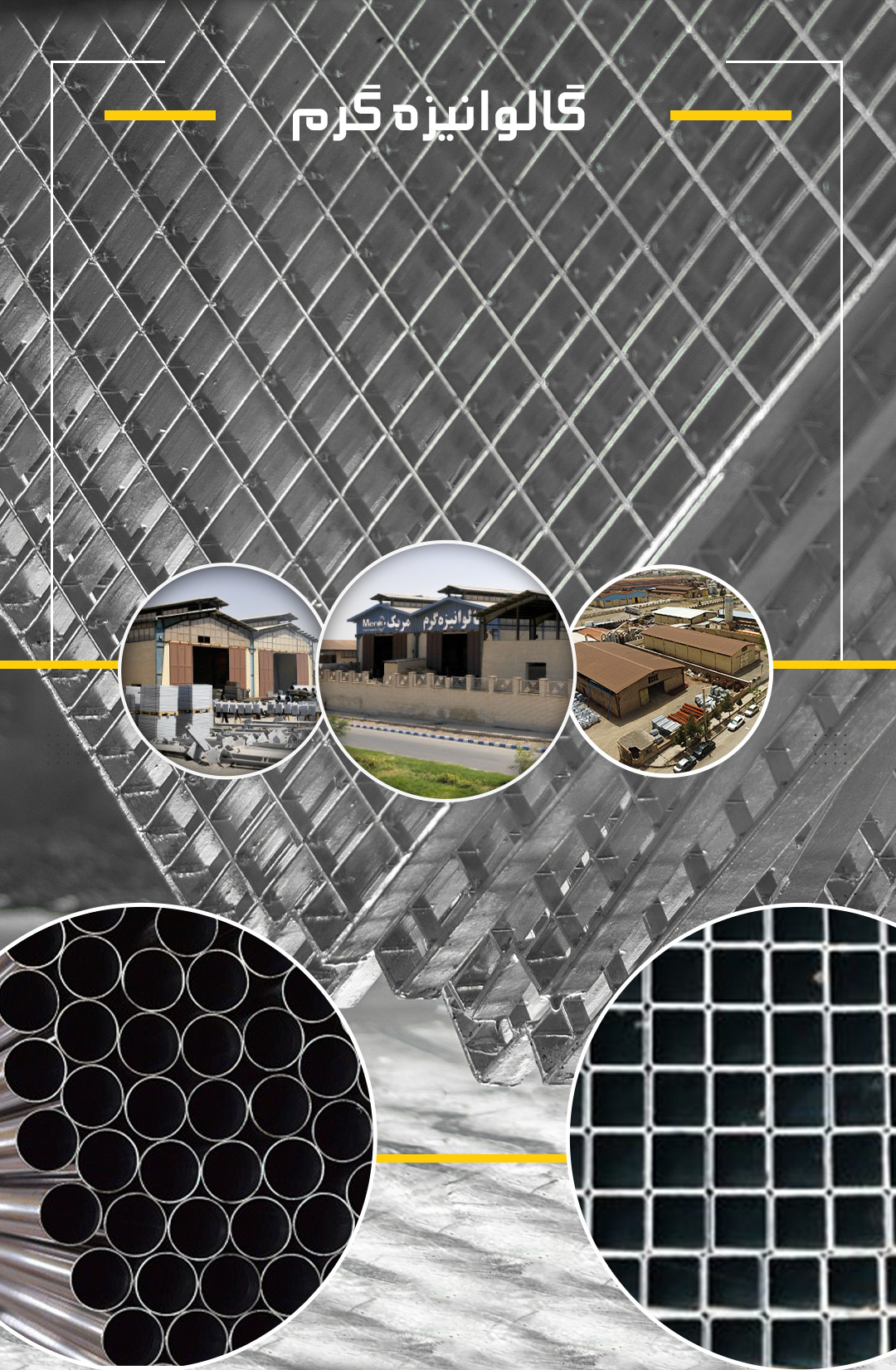
Hot-dip galvanizing unit of Merik Chemical Processing
Using the international standards of ASTM and EN, while having complete equipment and providing a quality guarantee with a production capacity of more than 30,000 tons per year, this unit is able to perform hot-dip galvanizing services of all kinds of metal structures. In order to increase quality, this group was honored to receive the national standard mark of galvanized coating in 2016.
Merik Chemical Processing Company is proud to carry out its activities with a customer-oriented perspective and at a competitive price, with a high speed in performing assigned tasks and providing products and services with the desired quality and in accordance with international standards.
Hot-dip galvanized unit equipment
Hot-dip galvanized unit equipment
-Chemical laboratory equipped to control the quality of raw materials and products
-Washing (pickling) preparation and preheating section
-Melting tub made by Pilling, Germany, with dimensions of 150*120*700 cm and 150*120*450 cm.
-The most modern temperature control and recording equipment
-Quality control department to perform all necessary tests, according to international standards
-Research and Development Department (R&D)
-Final section and Finishing packaging
- The chemical unit of this company, using experienced experts in the field of the production of consumables related to the preparation of pickling, has full supervision of the process of washing operations in the hot galvanizing line, which has improved the quality of the production parts and distinguished it from other competitors..
Warm Merik Galvanizing Services
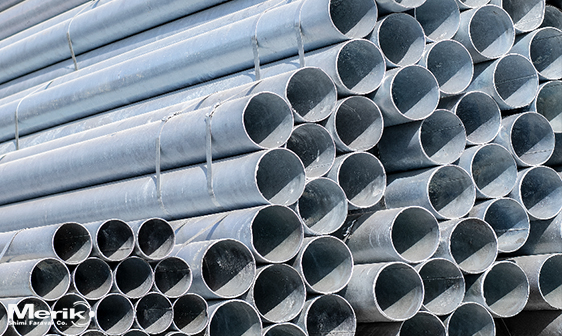
Galvanized all kinds of pipes and profiles in different sizes and thicknesses
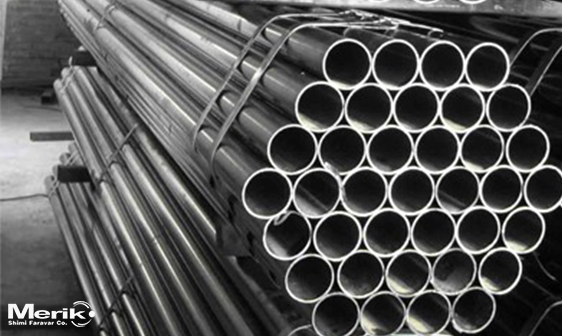
Galvanized all kinds of Manisman pipes in different sizes and categories
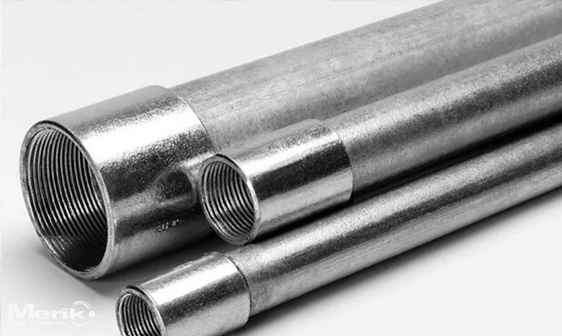
Galvanized all kinds of electrical pipes…
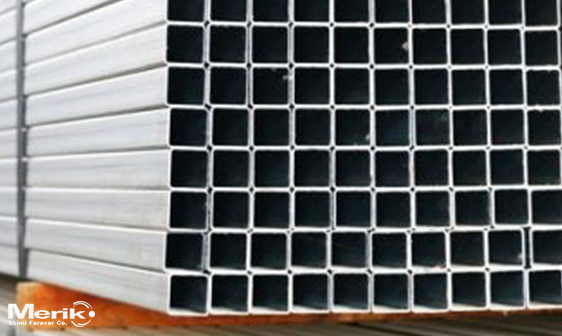
Hot galvanizing all kinds of profiles for greenhouse industries
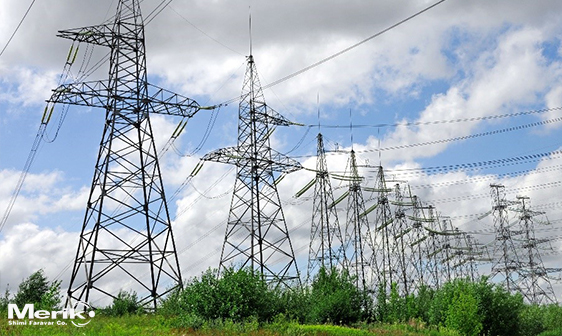
Galvanizing all types of power transmission, telecommunication and telescopic towers
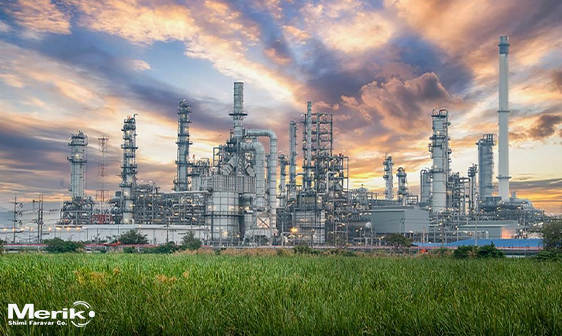
Hot galvanizing all kinds of equipment and metal structures used in refinery, petrochemical and power industries
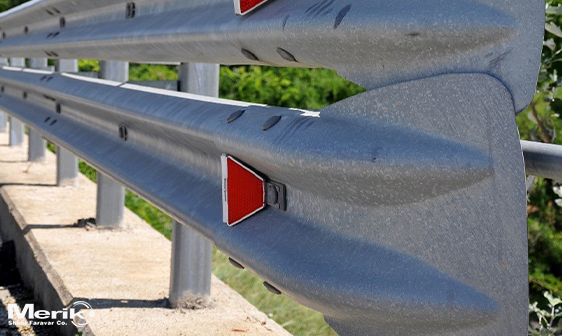
Galvanization of high pressure substation equipment, types of lighting bases, types of metal road structures (guardrails)
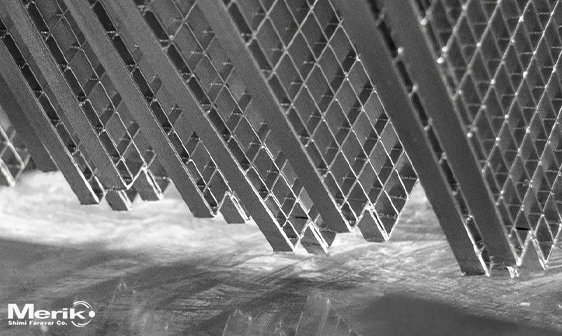